Steyrer Forschungsunternehmen zeigt auf Münchner Messe, was bei einer intelligenten Kombination von analogen und digitalen Drucktechnologien möglich ist.
STEYR/MÜNCHEN. Die Kunden erwarten von industriellen Produkten immer mehr Individualität. Das gilt nicht nur für die äußere Form, sondern auch für die Dekoration. Beim individuellen Bedrucken von klassischen Gebrauchsprodukten stoßen die Produzenten allerdings rasch an ihre technischen Grenzen. Das individualisierte Bedrucken von Gegenständen mit unregelmäßig gekrümmten Oberflächen ist mit bestehenden Drucktechnologien kaum möglich. PROFACTOR hat gemeinsam mit dem Tampondruckexperten ITW Morlock GmbH aus Deutschland mit einer Kombination von analogem Tampon- und digitalem Inkjet-Druck den Prototypen einer digitalen Tampondruckmaschine entwickelt, der richtungsweisend ist. Bei der Fachmesse „Inprint“ in München (12. bis 14. November 2019) wird das Modul am Stand der PROFACTOR (Halle A6, Stand 248), Member of UAR Innovation Network, präsentiert.
„Für einen Skischuh, eine Radkappe, eine Handyhalterung oder für eine nicht gleichmäßig geformte Vase, Optiken, Verpackungen bis hin zum Christbaumschmuck gab es bislang kaum Möglichkeiten für ein individuelles Bedrucken, das für den Konsumenten auch leistbar ist“, sagt Daniel Fechtig. Fechtig leitet bei PROFACTOR die Forschung rund um Funktionelle Oberflächen und Nanostrukturen. „Individuelles Bedrucken von Produkten wird von den Kunden zunehmend nachgefragt, sowohl von Einzelpersonen, die ihre Produkte mit Fotos, Namen oder Sujets dekorieren wollen, als auch von Unternehmen, die Alltagsgegenstände ohne großen Aufwand individuell branden lassen wollen.“ Beim klassischen Tintenstrahldruck erreicht man ob der plan angeordneten Druckköpfe bei gekrümmten Flächen kein zufriedenstellendes Druckbild. Analoge Tampons – vergleichbar mit „Stempeln“ – können gekrümmte Flächen zwar in guter Qualität bedrucken – allerdings erfordert jedes individuelle Design eine zeit- und kostenintensive Änderung des Klischees – der Druckmasken. Ein individuelles Bedrucken von Gebrauchs- und Konsumgütern zu marktfähigen Kosten ist damit natürlich nicht möglich.
Jahrelange Forschung und eine Kombination von digitaler und analoger Technik
PROFACTOR hat aufbauend auf jahrelanger Forschung Inkjet-Drucktechnologien gemeinsam mit ITW Morlock eine Lösung entwickelt, die bislang einzigartig erscheint. Sie verbindet digitale und analoge Technologien: Tampondruck und Inkjet-Druck werden intelligent kombiniert.
Das Tampon wird mit Tinte bedruckt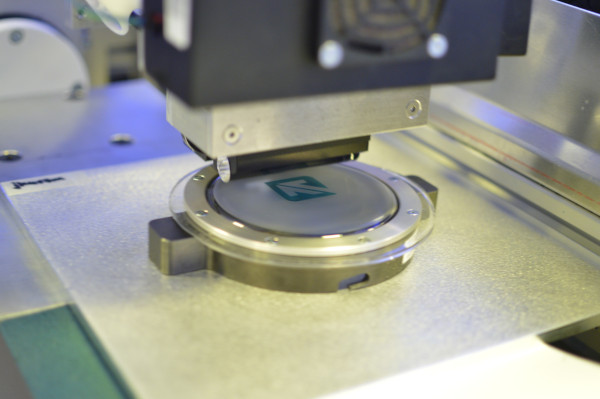
Der in Zusammenarbeit mit dem Industrieunternehmen ITW Morlock entwickelte digitale Tampondrucker funktioniert so: Das Tampon – der Druckstempel – ist eine transparente und dünne Silikonmembran aus UV-PDMS mit einer feinen Mikrostruktur. Sie wird in eine Halterung eingespannt und von einem Inkjet-Drucker mit den in digitaler Form vorliegenden Fotos, Texten oder Sujets in klassischem 4c-Druck beliebig bedruckt. Danach wird das Silikon aufgeblasen und mit dem zu bedruckenden Bauteil in der Maschine in Kontakt gebracht. Die auf diesem Weg aufgebrachte Druckertinte wird mittels UV-Licht ausgehärtet und vollständig auf das Bauteil übertragen. Die Membran wird danach abgezogen und ist innerhalb weniger Sekunden für einen neuen Druck mit beliebigem Inhalt bereit. „Das Ganze hört sich recht einfach an, aber zum Funktionieren müssen viele kleine Details berücksichtigt werden“, sagt Fechtig. „Die Entwicklung der geeigneten Tinten wird von spezialisierten Partnern übernommen, wir kümmern uns unter anderem um eine essenzielle Frage: wie löst sich die Tinte vollständig von der Membran und wie haftet die Tinte verlässlich auf den Bauteilen. Dafür sind unzählige Parameter zu berücksichtigen.“
Hersteller von Babyartikeln hat Interesse an diesem Verfahren
Das Modul wurde in Kooperation mit einem Babyartikel-Hersteller entwickelt. Fechtig: „Da kommt noch dazu, dass die Tinte selbstverständlich allen Normen für Sicherheit und Gesundheit entsprechen muss.“
Nach dem individuellen Dekor folgt: die individuelle Funktionalisierung
PROFACTOR-Geschäftsführer Christoph Breitschopf ist überzeugt, dass das digitale Tampondruck-Modul für Aufsehen sorgen wird: „Wir haben damit etwas entwickelt, dass einem produzierenden Unternehmen einen klaren Vorteil im Wettbewerb verschaffen kann. Das entspricht exakt unserer Unternehmensphilosophie.“ Die dekorative Individualisierung sei allerdings erst ein erster Schritt. Der Inkjet-Druck von elektronischen Bauteilen, RFID-Antennen, Sensoren oder Elementen wie Photovoltaik-Zellen mittels Inkjet-Druck und hochspezieller spezieller Tinten ist in den Labors bei PROFACTOR längst Realität. Breitschopf: „Mittelfristig sollten Konsumprodukte mit dem digitalen Tampondruck nicht nur vom Design her, sondern auch hinsichtlich intelligenter Funktion vom Konsumenten individuell konfiguriert werden können.“
Alternative: Roboterbasierter Inkjet-Druck
Eine Alternative zum digitalen Tampondruck ist der robotergeführte Inkjet-Druck. Auch hier forscht PROFACTOR seit Jahren daran, die Technologie so zu verfeinern, um von der Industrie genutzt zu werden. Fechtig: „Diese Methode bietet sich bei nichtstarren Gegenständen an, die für den Tampon-Druck nicht geeignet sind. Vereinfacht gesagt: Der digitale Tampondruck ist für das individuelle Bedrucken von starren Skischuhen geeignet. Der robotergeführte, kontaktlose Inkjet-Druck eignet sich besonders für das Bedrucken von großen Bauteilen und von z.B. weichen, nachgiebigen Turnschuhen oder Textilien.
Hier arbeitet PROFACTOR eng mit den Robotik-Spezialisten im Haus zusammen. Die größte Herausforderung ist das exakte Definieren des Pfades, den der Roboter um den in der Regel nicht per CAD-Daten exakt zu definierende Bauteil – wie eben ein Turnschuh – zurückzulegen hat. Derartige Produkte können mittels spezieller 3D-Software modelliert und digitalisiert werden. Für eine entsprechend hohe Druckqualität muss dabei aber noch an der Genauigkeit der 3D-Software gearbeitet werden.“