Die CREATIVE REGION hat mit dem Steyrer Forschungsunternehmen PROFACTOR ein europäisches Leuchtturmprojekt in der Höhe von 4 Mio. Euro an Land gezogen.
Gemeinsam mit weiteren PartnerInnen aus Deutschland, Spanien, Israel, Italien und der Schweiz sowie dem Linzer Unternehmen Haratech und der Kunstuniversität Linz wird im Rahmen des Forschungsprojektes Re-FREAM an den drei Standorten Linz, Berlin und Valencia an der Mode der Zukunft geforscht. Dort entwickeln in den nächsten drei Jahren KünstlerInnen, DesignerInnen und TechnikerInnen Produktionsmethoden, Materialien und Technologien für die Mode der Zukunft.
Forschungsprojekt stärkt Linz und Oberösterreich als internationalen Innovationsstandort
Positiv hervorzuheben ist neben der Höhe der generierten Fördersumme auch die verstärkte lokale Kollaboration zwischen Kunst und Industrie. Diese bewusst genutzte Schnittstelle soll ermöglichen, technische Neuerungen ressourcenschonend und gleichzeitig mit hohem ästhetischem Anspruch zu realisieren. Die Marktfähigkeit der Produkte ist dabei ein weiterer wichtiger Fokus des Projekts.
Stadträtin Doris Lang-Mayerhofer zeigt sich als Aufsichtsratsvorsitzende der Creative Region begeistert: „In Linz wird die Mode der Zukunft mitentwickelt. Mit dem internationalen Forschungs- und Förderungsprojekt Re-FREAM wird sich Linz als Fashion & Technology Standort in der Modewelt seinen Platz erarbeiten.“
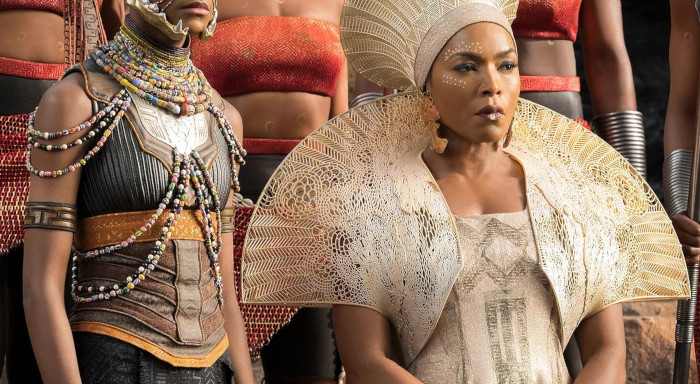
„Für die Wettbewerbsfähigkeit des Wirtschaftsstandortes OÖ ist es ausschlaggebend, wie gut es in Oberösterreich gelingt, Forschungsergebnisse in innovative Produkte und Dienstleistungen umzusetzen. Das Projekt Re-FREAM zeigt mit einem spannenden Themenfeld, wie es gelingen kann, dass ForscherInnen und KünstlerInnen neue Technologien gemeinsam entwickeln. Und PROFACTOR erweist sich einmal mehr als ein starker Partner in OÖ, um innovative Lösungen in die Wirtschaft zu transferieren. Das Projekt Re-FREAM ist aber zugleich ein gutes Beispiel für die Wirksamkeit der CREATIVE REGION: Sie agiert mit Spürsinn, um neue, innovative Themen und Zusammenhänge zu entdecken und die Kreativwirtschaft auf die Überholspur zu bringen.“, so Wirtschafts-Landesrat Markus Achleitner.
Reinhard Kannonier, Rektor der Kunstuniversität Linz: „Die Bündelung künstlerisch-kreativer Gestaltung und technologisch orientierter Forschung vor Ort, kombiniert mit internationaler Vernetzung, ergibt letztlich den „Rohstoff“ Innovation. Ihn braucht die Region und ganz Europa, um in der rasant fortschreitenden Globalisierung nicht nur zu bestehen, sondern neue Richtungen vorzugeben zu können.“
KünstlerInnen und DesignerInnen als DisruptorInnen
Die Modeindustrie gilt als eine der schnelllebigsten Industriebranchen, die außerdem komplexe Arbeitsschritte und Lieferketten beinhaltet. Die traditionellen Arbeitstechniken und hochkomplexen Prozesse bieten Raum für Innovation; besonders, wenn durch interdisziplinäre Ansätze KünstlerInnen und DesignerInnen herkömmliche Herangehensweisen mit neuen Blickwinkeln betrachten. Neue digitale Technologien wirken sich sowohl auf Entwurfsprozesse, Produktion aber auch die Distribution und Präsentation von Mode aus.
URBAN MANUFACTURING als Potential für die Mode der Zukunft
Ein wichtiger Beweggrund für die Projektgenehmigung war der Ansatz, die Bekleidungsproduktion der Zukunft wieder nach Europa zurückzuholen. Urban Manufacturing ist dabei relevantes Schlagwort: Es sieht die Stadt als neuen Produktionsraum, in welchem hochwertige, designorientierte Produkte entstehen. Zudem schafft Urban Manufacturing eine neue Nähe zwischen ProduzentInnen und KonsumentInnen, die heute genau wissen möchten, wo und wie ein Produkt hergestellt wird. „Vor allem für die Mode bietet Urban Manufacturing die große Chance, eine Alternative zur viel kritisierten Produktion in Billiglohnländern zu schaffen. Dies ist heute durch neue Technologien möglich, welche derzeit nicht nur die Mode selbst, sondern auch die Art und Weise, wie diese gestaltet und produziert wird, verändern.“ so Christiane Luible-Bär, Projektpartnerin und Co-Leiterin der Abteilung fashion & technology an der Kunstuniversität Linz.
Christoph Breitschopf (CEO PROFACTOR): „In den drei Innovationhubs Valencia, Berlin und Linz wird an drei wichtigen Fragestellungen der Mode der Zukunft gearbeitet: Nachhaltigkeit, elektronische Textilien sowie 3D-Druck. In zwei Ausschreibungen sucht das Projekt KünstlerInnen und DesignerInnen, die mit bahnbrechenden Ideen gemeinsam mit ForscherInnen bestehende Technologien weiterentwickeln. Dabei werden zwanzig Forschungsprojekte gefördert.“
KünstlerInnen und DesignerInnen können sich ab März bewerben
Im März startet die Ausschreibung für die insgesamt zwanzig Projekte. Die Calls sind mit bis zu 55.000 Euro pro Projekt dotiert und werden von einer fachkundigen Jury ausgewählt. Die erfolgreichen Einreichungen werden dann in den drei Hubs im Rahmen eines Co-Creation Prozesses professionell begleitet. Die ausgewählten KünstlerInnen und Creators haben so die Chance, gemeinsam mit ForscherInnen die Mode der Zukunft zu revolutionieren.
Die Mode der Zukunft ist smart und urban – und kommt aus dem 3D-Drucker
Die drei Hubs in Valencia, Berlin und Linz bauen in ihren jeweiligen Schwerpunkten das Ökosystem der städtischen Modeproduktion auf. Sie vernetzen Technologieanbieter, Unternehmen, Kreativ- und Kunstzentren sowie Produktionsstätten. Außerdem bieten sie Innovationsräume für Exploration, Kreativität, Kleinproduktion, Wissens- und Innovationstransfer an Modedesigner und -macher. Besonders 3D-Druck spielt eine wichtige Rolle – denn dieser ermöglicht auch die Produktion von umweltfreundlichen und elektronischen Textilien, die für smarte Mode relevant sind.
Beispielhafte Vorreiterin aus Österreich, hochkarätige Jury
Ein aktuell herausragendes Beispiel für innovatives, österreichisches Modedesign ist die Designerin Julia Körner. Sie ist bekannt für innovative Produktionstechniken und gilt als eine der weltweit führenden Köpfe in digitalen Fertigungsmethoden und 3D-Druck. Sie arbeitet interdisziplinär in den Bereichen Architektur, Produkt- und Modedesign. Ihre Arbeiten wurden international ausgezeichnet und vielfach publiziert. Ihre jüngsten Kooperationen sind 3D-gedruckte Modestücke, die mit namhaften Haute Couture Häusern für Pariser Modewochen entwickelt wurden sowie die 3Dgedruckten Kostüme für Marvel’s Hollywood Film Produktion ‚Black Panther‘ (siehe Bild). Julia Körners innovative Ansätze im Modedesign und die einzigartigen Kooperationen mit Unternehmen zeigen, wie wichtig der Einfluss neuer zukunftsorientierter Technologien im Feld der Mode ist. Auch die Re-FREAM Jury wird mit hochkarätigen VorreiterInnen besetzt sein; unter anderem wird der Schweizer Produktdesigner Christophe Guberan die Einreichungen bewerten. Er denkt Produktionsprozesse neu und setzt außergewöhnliche Techniken und Materialien für seine Entwürfe und Projekte ein; seine „LIQUID PRINTED BAGS“ , welche in Kollaboration mit dem MIT Self-Assembly Lab entstanden, werden mittels 3D-Schnelldruckverfahren in einer Gelemulsion hergestellt. Diese Methode ermöglicht schnelle und qualitativ hochwertige Ergebnisse, die neue Dimensionen für die Möglichkeiten des 3D-Drucks setzen.
Re-FREAM forscht in den nächsten drei Jahren an der Mode der Zukunft
Innovationen sind in vielen Bereichen möglich – jene zwanzig Projekte, die ab März gesucht werden, werden einen hohen Innovationsgrad aufzeigen müssen, um von der unabhängigen Fachjury in die finale Runde gewählt zu werden. Denn so viel ist klar: Mode wird künftig virtuell designt und probiert werden, lokal produziert und dem Kunden in kurzen Wegen und dabei zeitnah geliefert werden. Sie wird nicht nur mehr aus zweidimensionalen Textilien produziert werden, denn 3D-Scan und 3D-Druck eröffnen ganz neue Wege, komplexe Formen zu entwerfen und zu erstellen: Willkommen in der Maßschneiderei der Zukunft, wo individuell und ressourcenschonend auf die Körpermaße der KonsumentInnen eingegangen werden kann. Die Reaktionsfähigkeit der Textilien ist ein weiterer möglicher Innovationsfaktor: Integrierte Elektronik macht Kleidung programmierbar und leitfähig. Diese technologischen Neuerungen werden Einfluss auf die Modeindustrie und deren Zulieferungsketten haben. DesignerInnen und KundInnen werden direkter miteinander in Verbindung treten. Faktoren und Kriterien wie diese werden für die Auswahl der Projekteinreichungen ausschlaggebend sein. KünstlerInnen und DesignerInnen können sich ab März bewerben. „Es freut uns, dass wir mit Re-FREAM die Leaderposition für ein herausragendes und innovatives EU-Projekt übernehmen. Wir erwarten zahlreiche Bewerbungen und werden in den nächsten drei Jahren gemeinsam mit unseren internationalen ProjektpartnerInnen länderübergreifend an innovativen, marktfähigen Produkten arbeiten.“, so Patrick Bartos, Geschäftsführer der CREATIVE REGION Linz & Upper Austria.
Projekname: Re-FREAM (Re-FREAM: Re-Thinking of Fashion in Research and Artist collaborating development for Urban Manufacturing)
Förderung H2020 – ICT-32-2018 – STARTS – The Arts stimulating innovation
Laufzeit Dezember 2018 – November 2021
Projektpartner
- Creative Region Linz& Upper Austria GmbH
- PROFACTOR GmbH
- Associacion de Investigacion de la Industria Textil
- Wear-it Berlin GmbH
- Care Applications, S.L.U
- INSTITUTO EUROPEO DI DESIGN SL
- CONSORZIO ARCA- CONSORZIO PER LA PROMOZIONE DELLE APPLICAZIONI DELLA RICERA E LA CREAZIONE DI AZIENDE INNOVATIVE
- HARATECH GmbH
- UNIVERSITÄT FÜR KÜNSTLERISCHE UND INDUSTRIELLE GESTALTUNG LINZ
- STRATYSYS LTD
- FRAUNHOFER GESELLSCHAFT ZUR FÖRDERUNG DER ANGEWANDTEN FORSCHUNG E.V.
- EIDGENÖSSISCHE MATERIALPRÜFUNGS- UND FORSCHUNGSANSTALT