Derzeit ist der Einsatz von Biokompositen auf weniger kritische Anwendungen beschränkt, die keine besonderen Anforderungen an die mechanische Leistung stellen. Die Verwendung von synthetischen Verbundwerkstoffen aus Kohlenstoff- oder Glasfasern weist jedoch einige Schwierigkeiten hinsichtlich des Recyclings und der Abhängigkeit von Drittländern auf. Etwa 98 % dieser synthetischen Verbundwerkstoffe landen immer noch auf Mülldeponien und etwa 80 % der Rohstoffe werden derzeit außerhalb Europas hergestellt.
Um diese Situation zu verbessern, befasst sich das Projekt BioStruct mit den Herausforderungen beim Einsatz von Biokompositen für Strukturbauteile und zielt darauf ab, das Anwendungsspektrum von Biokompositen zu erweitern.
Dies wird durch die Entwicklung eines präzisen Drapierungsprozesses zur Steuerung der Faserausrichtung, durch die Erstellung von Materialmodellen, die die natürliche Variabilität des Materials erfassen, und durch die Integration nanostrukturierter, biobasierter Sensoren zur Überwachung der Bauteile im Einsatz erreicht. Durch die erhöhte Genauigkeit und durch zusätzliche Regelkreise im Herstellungsprozess werden die gewünschten Eigenschaften und eine konstante Qualität erreicht.
Im Rahmen dieses Projekts werden Anwendungsfälle aus der Windenergie und dem Bootsbau untersucht, mit dem Ziel, ein Rotorblatt in Originalgröße und einen Schiffsrumpf herzustellen, um die technische Machbarkeit zu demonstrieren und TRL7 für die Fertigungstechnologien zu erreichen.
Das Konsortium besteht neben den Endanwendern aus Partnern aus den Bereichen Automatisierung, Maschinenbau, Messtechnik, Materialherstellung und Simulationssoftware, um alle Aspekte der Entwicklungen abzudecken. Basierend auf dem prognostizierten Wachstum des Biokompositmarktes, der bis 2030 voraussichtlich um den Faktor 2,5 zunehmen wird, erwartet das Konsortium bis 2030 ein Marktpotenzial von etwa 100 Mio. €.
PROFACTOR übernimmt nicht nur die Projektkoordination inklusive Daten-, Risiko- und Innovationsmanagement, sondern konzipiert, konstruiert und baut den Sensor zur Inspektion von Naturfasermaterialien. Die Adaption einer bestehenden Drapier-Roboterzelle für den Einsatz mit Naturfasermaterialien sowie die Konstruktion, Entwicklung und Herstellung eines Sensors zur Überwachung der produzierten Strukturbauteile im Einsatz sind weitere Aufgaben, die durchgeführt werden.
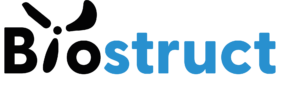
Projektname: BioStruct
Projektwebseite: www.biostruct-project.eu/
Förderung: HORIZON-IA
Projektvolumen: €5,495,530
Laufzeit: 01 Jan 2024 – 31 Dec 2024
Projektpartner:
- PROFACTOR GmbH: Coordinator (www.profactor.at)
- NOMA Resins SP zoo (www.noma.com.pl/)
- Reparaciones Nauticas Amura SL (www.amurasl.com/)
- Enginsoft SPA (www.enginsoft.com/)
- Fundacion CIDETEC (www.cidetec.es/es/inicio)
- Association Techtera Auvergne Rhône Alpes (www.techtera.org/en/)
- IDEKO S Coop (www.ideko.es/)
- Bladeworks SRL (www.cartflow.com/)
- Abele Ingenieure GmbH (www.abele-ingenieure.de/)
- Lumoscribe ltd (www.lumoscribe.com/)