Currently, the use of bio-composites is limited to less critical applications that do not have significant requirements in terms of mechanical performance. However, the use of synthetic composites made from carbon or glass fibre has several difficulties in terms recycling and in terms of dependence on third countries. About 98% of these synthetic composites still end up in landfills and about 80% of the raw materials are currently manufactured outside of Europe.
To improve this situation, the project addresses the challenges of using bio-composites for structural parts and aims to increase the range of applications in which bio-composites can be used. This will be achieved by developing an accurate draping process to control fibre orientation, by creating material models that capture the natural variability of the material and by integrating nano-structured, bio-based sensors for load monitoring. Through the increased accuracy and additional control loops in the manufacturing process the consortium expects to achieve predictable properties and constant quality.
Within the project use cases from wind energy and boat-building will be investigated, aiming at the manufacturing of a full size rotor blade and a ship hull to demonstrate the technical feasibility and achieving TRL7 for the manufacturing technologies. In addition to the end users, the consortium consists of partners from automation, machine building, measurement technology, material manufacturing and simulation software to cover all aspects of the developments. Based on the predicted growth of the bio-composites market, which is expected to increase by a factor of 2.5 by 2030, the consortium expects a market potential of about 100M€ by 2030.
PROFACTOR will not only take care of the Project coordination including the data-, risk- and innovation-management but will also design, construction and build the hardware setup of a sensor for the inspection of natural fibre materials. The adaption of an existing draping robot cell for the usage with natural fibre materials and the design, development and manufacturing of a load sensor are additional tasks that will be carried out.
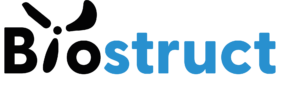
Project name: BioStruct
Project website: www.biostruct-project.eu/
Funding: HORIZON-IA
Project volume: €5,495,530
Project duration: 01 Jan 2024 – 31 Dec 2024
Project partners:
- PROFACTOR GmbH: Coordinator (www.profactor.at)
- NOMA Resins SP zoo (www.noma.com.pl/)
- Reparaciones Nauticas Amura SL (www.amurasl.com/)
- Enginsoft SPA (www.enginsoft.com/)
- Fundacion CIDETEC (www.cidetec.es/es/inicio)
- Association Techtera Auvergne Rhône Alpes (www.techtera.org/en/)
- IDEKO S Coop (www.ideko.es/)
- Bladeworks SRL (www.cartflow.com/)
- Abele Ingenieure GmbH (www.abele-ingenieure.de/)
- Lumoscribe ltd (www.lumoscribe.com/)